The Top 5 Reasons Why Your Engine Won’t Start
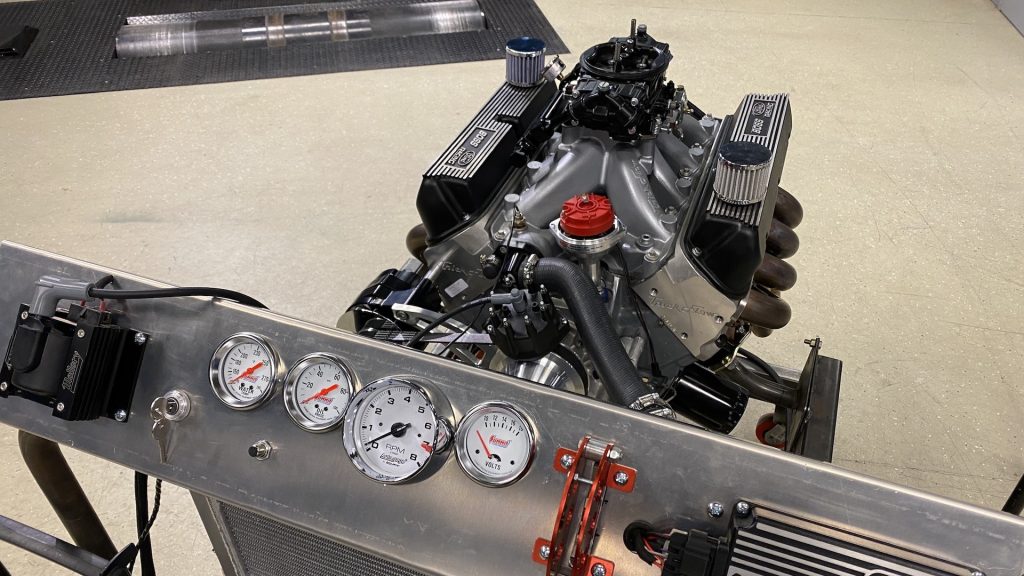
Whether you’re a beginner engine builder or you’re a seasoned pro, sooner or later you are going to run into an issue in which the engine won’t start. We’ve all heard of Murphy’s Law: anything that can go wrong will go wrong. It is an inevitability and it happens to everyone.
Depending on the engine, troubleshooting can be a pain and sometimes drive you nuts trying to figure out the cause. So to help ease your worries and future stress, we listed the Top 5 Reasons Why Your Engine Won’t Start, how to diagnose each problem, and how to solve them.
Reason 1: Air (or lack thereof)
At first, you may think, “How can air be an issue when we’re surrounded by it all the time? It’s not like we’re building these engines underwater.” But airflow is as essential for an engine’s performance as it is for you to breathe. Any sort of block or restriction can hinder that airflow, causing your engine to suffocate and eventually not work.
Say if your engine does work, but it won’t be able to stay running for long, it may be due to an air issue as well. The solution could be as simple as the throttle blades being too closed, preventing ample amounts of air to flow through the engine.
Another common problem area related to hindered air flow is clearing the air filter or intake tract of any dirt, bugs, and debris. Not unclogging your air filter can lead to your engine running poorly and being low on power. The same can be said if someone oils a non-oilable air filter element, which can be a tricky air restriction problem to find.
These days we commonly see older rides get outfitted with newer engines with direct injection. The problem that can arise with high-mileage cars is that large amounts of carbon can be found caked on the inside of the intake valve. Sure, the car will still be able to operate and drive, but the engine will still be underperforming.
Reason 2: Fuel
Having enough fuel sounds like the basics of the basics, but sometimes it can be too easy to overlook. Because you would be amazed by the number of times people have torn their engines apart only to find out that the reason why it wasn’t starting was because it had no fuel. A faulty fuel gauge can be a very fickle thing.
It is always wise to have the right kind of fuel for your engine. If you’ve got a gas-powered engine, don’t put diesel in it. The same goes for race engines, which need to be filled with race engine fuel, not regular pump gas. Confirming that there is the right fuel in the fuel tank is the first box to check.
But say there is gas in the fuel tank and the engine still isn’t running. The next thing you should check before diagnosing a fuel system problem is to check the fuel pressure gauge. A carbureted engine should have its fuel pressure gauge in its fuel log or in the fuel regulator. On an engine with EFI (Electronic Fuel Injection) it can usually be placed in a rail or in a pressure tap where you can insert a mechanical gauge to check the pressure.
- A mechanical-style fuel system has a fuel pump that is usually bolted to the engine, and there’s an eccentric on the camshaft that runs an arm or pushrod which runs a diaphragm in the pump. That diaphragm’s actuator is what pulls in fuel from the tank. If fuel is not making its way to the gauge, then something is wrong with the system.
- One reason could be that the pump’s lines are installed backward. If the inlet is hooked into the outlet side and vice versa, then fuel will not get pumped into the carburetor.
- Another could be because either the diaphragm and/or actuation are not working. Sometimes older ones can wear themselves out over time and need to be replaced. Note: some aftermarket pumps may generate excessive amounts of pressure and they need to be regulated down.
- An EFI system has a different set of components when compared to a mechanical style. Every EFI system is fed by an electric fuel pump, and some carbureted systems can be as well. If your mechanic gauge is reading “no pressure”, you may want to see if the pump is actually running.
- Always make sure that your wiring is correct, you are running good power, you have good ground, and make sure that the pump hasn’t been installed in reverse. Most pumps indicate which direction is for flow, so don’t be afraid to double-check before installing them.
- If the pump is set in the right direction is running, and the engine still won’t start, check the fuel filters. Make sure that these filters are clear of any dirt, debris, rust, or foam. A clogged filter can prevent most, or any fuel from flowing through the fuel system.
- Lastly, what are the conditions of the lines? Fuel pressure problems can arise if they have rust in them, or are kinked out of shape to some degree. It is also wise not to use rubber lines because mixing them with a steel line can risk the rubber being torn internally and restrict flow. It may work fine while idling, but the second it gets under load the fuel demand goes up and the pressure goes down. This is why when making new lines you always make sure your lines are fully cleared of any unwanted debris and blow them out completely with air before running fuel through them. Because if more dirt and debris get sent through your fuel filter, you are going to wish you checked earlier.
Reason 3: Spark
While fuel systems are generally simple with a few variations, the ignition system can be a little more complicated. But first things first, how do we check for spark? The best way to do it is to physically take a spark plug, remove it from the cylinder head, have it connected to the system, have it grounded on the engine, and then turn the engine over and visually look for any spark. If there is no spark, it’s time to check to see if the battery is healthy. Diagnosing issues with the electrical system can be extremely difficult if your battery is no good. A fully-charged battery will be a lot more helpful when it comes to narrowing down the issue with the ignition system.
For a Distributor Type Ignition System with a CDI box and Coil:
- The first component to check is the pickup found in your distributor. Every time the reluctor inside the distributor passes over the pickup, it receives an AC signal to give the ignition box the RPM signal and the correct time to fire the coil. In order to tell if pickup is working correctly, the engine needs to be rotating to check for AC voltage. If it isn’t generating that AC signal, it could mean that you’ve got a faulty pickup.
- The ignition box is the next component to examine. Basically, it acts as the middleman between the distributor and the coil. It receives the AC signal from the distributor and then relays that signal to the coil to fire. So long as it has a 12V keyed ignition, 12V power and ground from the battery, and receives the AC signal from the distributor, then your ignition box should be sending a signal to the coil. But if it isn’t, and your wiring is good, then your ignition box could be malfunctioning.
- The coil itself is pretty easy to diagnose because they are very simple. You can test it on the primary and secondary windings for resistance if you know the values that you are looking for. Another option if there’s no spark is checking to see if the coil has a 12V keyed ignition to the positive side and a triggered ground that is being triggered by the ignition box on the negative side. If it’s yes for both and there is still no spark, then you probably have a bad coil.
- Lastly, there are the spark plugs themselves. These can be easily overlooked sometimes because they are seen as just a simple part. But in order for a spark plug to be fully functional, then there cannot be any damage to it whatsoever. So, it is always wise to inspect every new and used spark plug before using them in your engine. That means no cracks in the porcelain, the ground strap isn’t touching the center electrode, and the gap is set for your application. If there is any sort of bump or physical impact to your spark plug, it will have more use in the garbage can than in your engine.
While these are the four of the primary components involving your engine’s ignition system, there are some other potential causes for an engine that won’t start even if it does have spark.
- Make sure your distributor is installed correctly
- Make sure your wiring is installed correctly
- More sure your plug wires are firing in the correct order
- Check every plug wire with an Ohm meter
Reason 4: Compression
Internal-combustion engines need compression so the air-fuel mix will be able to ignite easier, causing it to produce the power necessary to operate a vehicle.
There are only a few ways in which the air-fuel mixture can escape from the engine, and you can conduct these tests to determine if, and where, any compression has been lost:
- The first is a Cylinder Leak-down Test. Chances are your junkyard engine project doesn’t have a starter on it for you to crank over and this test can be done without having to crank the engine. First, remove the spark plug wire and the spark plug from the cylinder and set that cylinder at TDC on compression stroke. Then we can connect the hose from our Cylinder Leakage Tester to the cylinder and connect it to 100 PSI regulated shop air. The gauge will give us a readout and tell us how much of the air mix is escaping the cylinder. Anything under 20% leakage is considered good and anything under 10% is great. If there is excessive leakage, you can listen to the intake, exhaust, and crankcase to determine where its leaking to.
- The next is a Cranking Compression Test. For this, we need to remove all the spark plug wires and spark plugs. We will then insert the hose into one cylinder at a time and crank the engine over until the pressure reading on the gauge stops increasing. For stock/performance engines pressure readings between 150 and 180 PSI mean we will be in good shape and every cylinder should have relatively similar results. But should you receive an unsatisfactory reading, chances are there is something mechanical happening inside your engine that is hindering its ability to build compression.
With junkyard engine builds, time and mother nature can take its toll by causing the valves to stick. Even if the engine turns over, there won’t be any compression happening. There could also be a completely separate mechanical failure preventing any compression from being formed in the engine. So, it’s wise to make sure everything is operating properly before attempting to start a take-out engine.
Meanwhile, with a new engine build, sometimes you won’t be getting any compression because you have the wrong parts, or parts were installed incorrectly, causing valves to hang open and no compression to be made.
Reason 5: Operator Error
Everyone makes mistakes, so it shouldn’t come as a surprise that you (or someone else) made a mistake during the building process. It happens to all of us and can cause some of the biggest headaches for anyone. That is why it is always great to have another set of eyes take a look at your work, because they might notice something that you could have overlooked.
As they say, two heads are better than one!
Want to read more articles like this?
Join the PowerNation Email NewsletterRead More from PowerNation
- Chapters
- descriptions off, selected
- captions off, selected
This is a modal window.